Awards
Our Commitment to Your Success
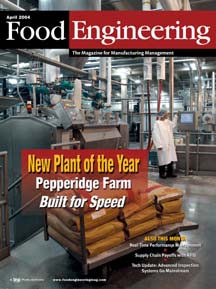
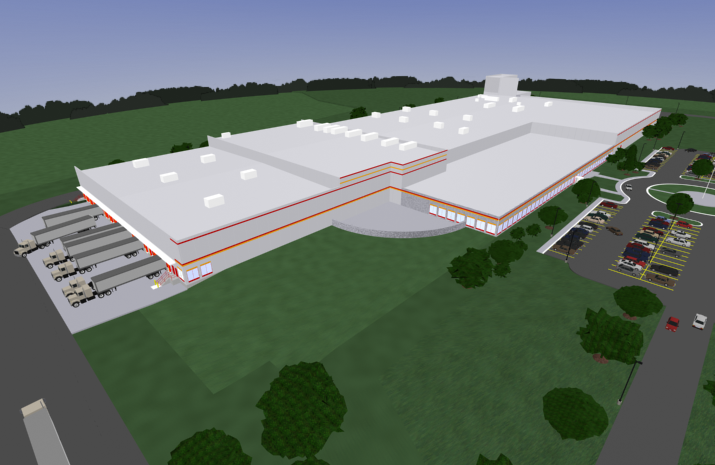
Food Engineering Magazine – Plant of the Year
Pepperidge Farm – Bloomfield, Connecticut
Facility Group/FDG provided architectural, engineering, and construction services on the 290,000-SF greenfield “hot” bakery project. Modernization and strategic location analysis drove this project. Three new production lines and one relocated production line would produce a variety of baked bread products.
Unit operations for the project include bulk material receiving, storage silos, pneumatic transfer of material, major-minor handling systems, mixing, proofing, baking, wrapping, packaging, and storage.
The central utilities corridor doubled as a visitor gallery, allowing viewing of the various production areas without having to enter the processing space.
Two mixing operations per line allow for maximum efficiency for the overall line. Automated pan handling and basket washing limited the need for too much labor associated with these activities.
Centralized utilities were planned for individualized metering on a per line basis. This information was fed back to the central control room for reporting and control.
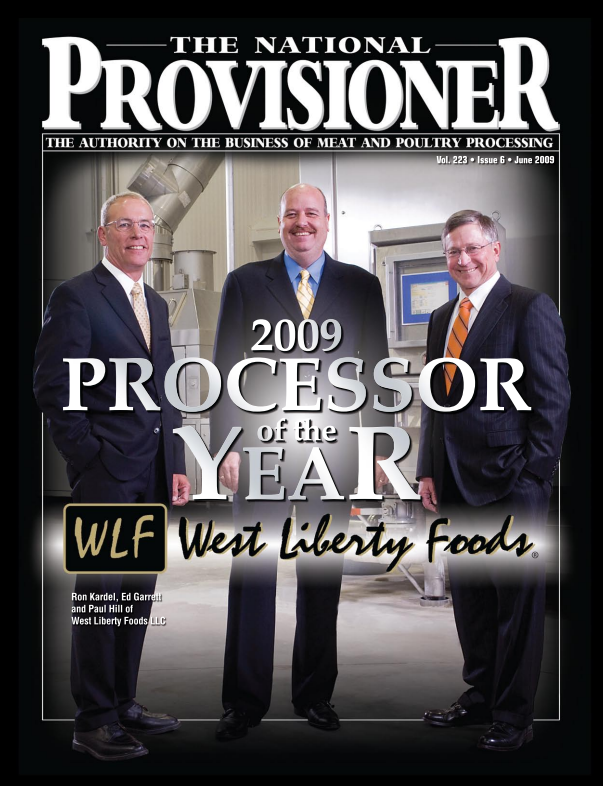
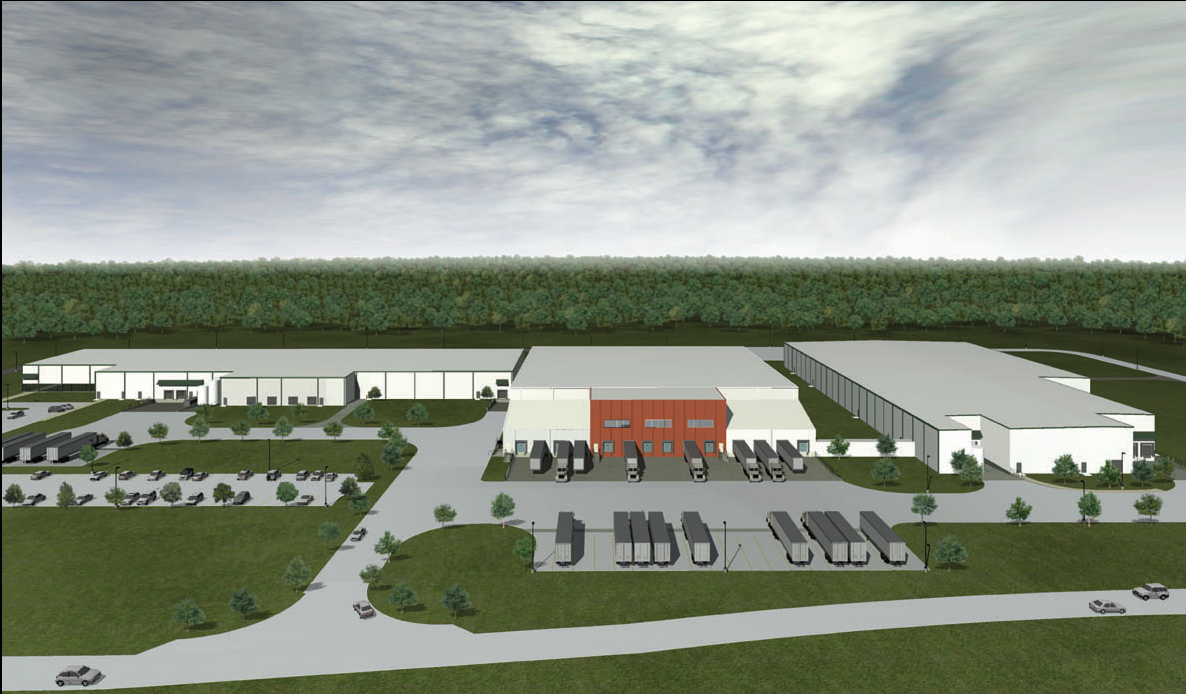
Food Engineering Magazine – Fabulous Food Plant
The National Provisioner – Processor of the Year
West Liberty Foods – Tremonton, Utah
Facility Group/FDG provided architecture, engineering, program management, and construction services for a facility to produce a full line of RTE (Ready to Eat) slicing logs and batter breaded and fried RTE chicken. The facility comprises of approximately 70,000 SF of process and process support areas plus the requisite amount of employee welfare facilities for both raw and cooked on a second floor. The slicing facility includes approximately 110,000 SF of process and process support areas plus the requisite amount of employee welfare facilities on a second floor.
Total product capacity for the maximized Tremonton facility is approximately 1 million pounds of sliced products and 700,000 pounds of chicken products weekly. There is room to accommodate the expansion of the RTE chicken to double the original capacity. The balance of the plant is designed to be readily expandable to meet the future needs of West Liberty Foods.
The further processing area can produce both raw and Ready-To-Eat items. This area was designed to completely segregate the raw and cooked sides of the process. Each “side” is complete with its own employee welfare areas to ensure the absolute segregation of raw and cooked.
Slicing logs delivered from the manufacturing plant are off loaded into the rack cooler. This area has the highest relative pressure in the facility to prohibit bacterial influx from the outlying areas of the plant. The products are sliced into various customer dictated configurations.
As a recognized leader in the industry for food safety and innovate process efficiently, this project for West Liberty Foods was featured in the December 2008 issue of Food Engineering Magazine as a “Fabulous Food Plant.” West Liberty Foods was also recognized as “2009 Processor of the Year” by The National Provisioner.

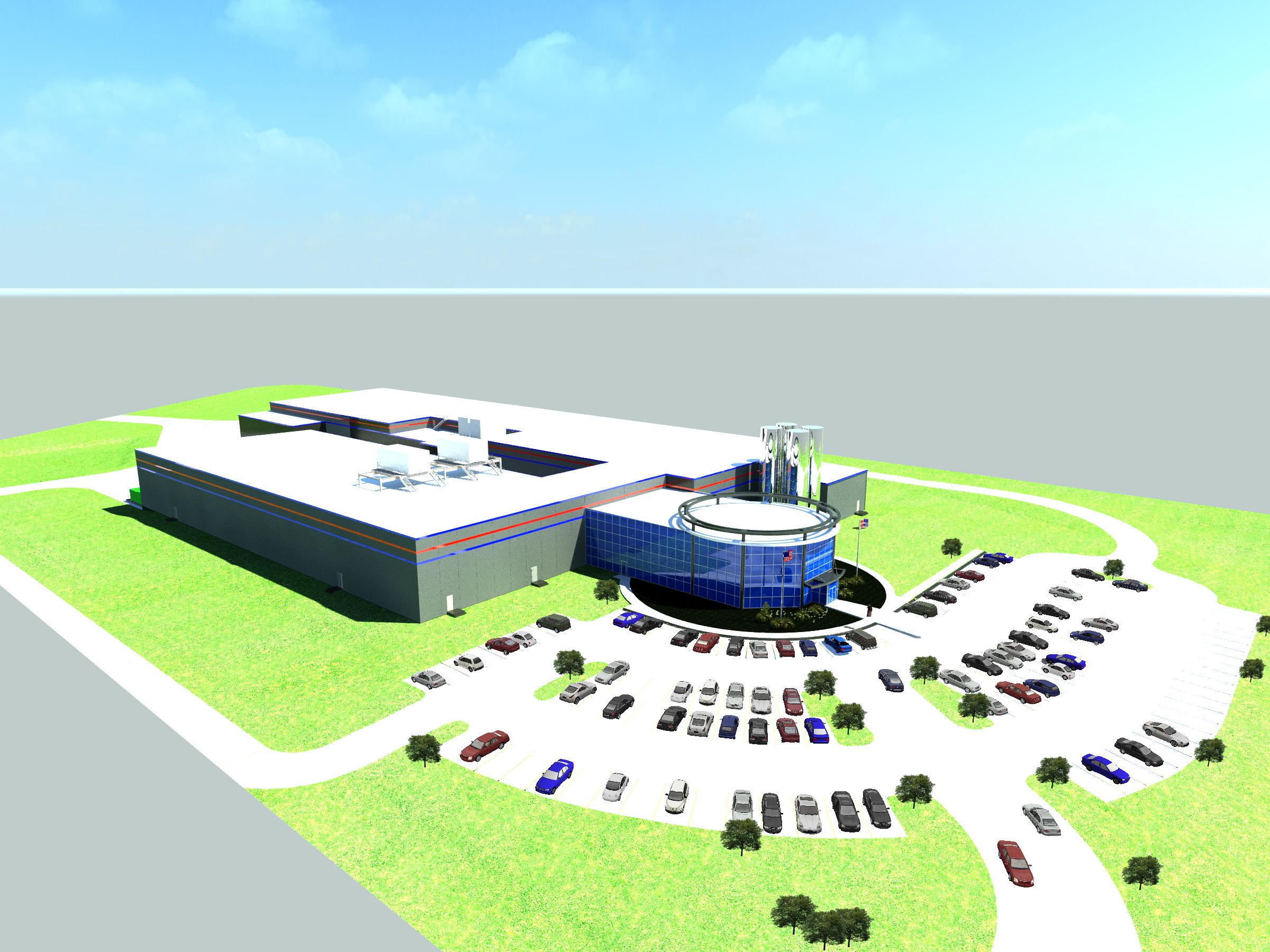
Food Engineering Magazine – Sustainable Plant of the Year
Plumrose USA – Council Bluffs, Iowa
Teaming with Plumrose USA, Facility Design Group provided the architecture, engineering, and program management services for one of the most technologically advanced and food safe process operations in North America. Plumrose, with $500 million in sales and 1,450 employees nationwide, believes in investing in the future of its business. Recognized as the number one supplier of retail private brands in the United States for sliced lunch meats, the 75-year-old company opened a new $78 million, 125,000 square feet, state of the art and highly sustainable LEED Silver certified, sliced lunch meat facility in October 2012 to meet the needs of tomorrow’s customers. The innovative design of the facility’s processes improves production planning and adds roughly 25 percent production capacity to Plumrose’s overall output. Owned by the Denmark-based company Danish Crown, Plumrose manufactures a variety of packaged meat products, including sliced deli meats, bacon, and canned meats.
This new facility was selected as the 2013 Sustainable Food Plant of the Year by Food Engineering Magazine.
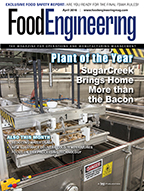
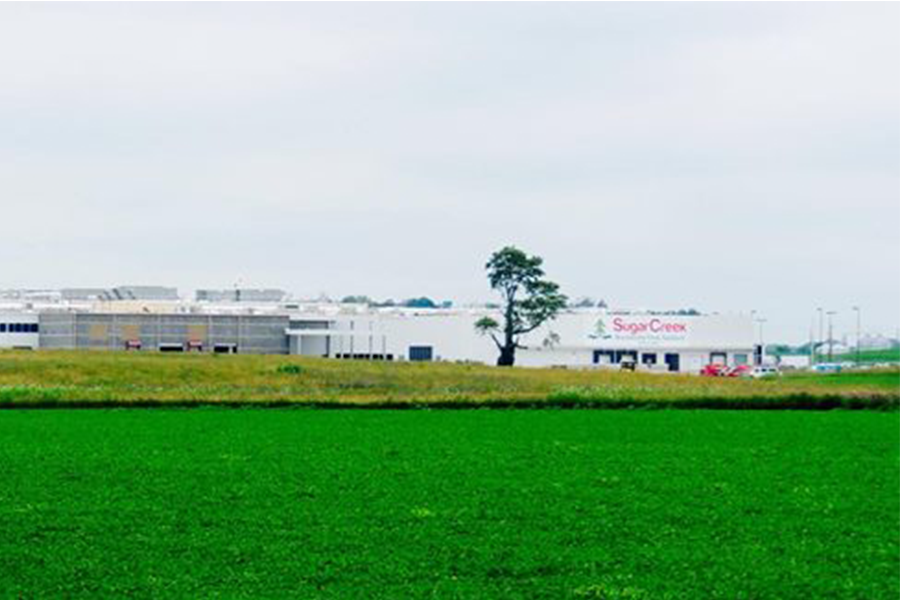
Food Engineering Magazine – Plant of the Year
Sugar Creek – Cambridge City, Indiana
FDG collaborated with Sugar Creek from the start of the Planning process. The goal was to integrate receiving raw product into an existing facility Sugar Creek had purchased. Food Safety drove all design decisions. Raw Meat products receiving and product blending together with handling work in progress (WIP) was studied to determine how different raw material would be received, blended, sorted for the different cooking operations envisioned for the plant. The facility plant layout was driven based on separation of raw, WIP, Blending, Cooking, Packaging, and Shipment of finished product. The final design layout required extensive meetings between FDG and Sugar Creek personnel for all parties to agree on a design that met the objective of food safety and employee separation by raw, cooking, and packaging halls.
The new Cambridge City facility, completed in August 2015, is designed to enable human capital to be as productive as possible by enabling a highly Engaged Workforce and the use of Lean flow principles.
- A comprehensive hydrology and hydraulics study to provide onsite storm water management that also provided storm water quality benefits. A new storm water pipe network was designed for the site that allowed valuable space occupied by the ditches that were needed for the project’s improvements to be filled while safely conveying offsite storm water drainage thru the site.
- A new truck entrance near the south end of the site that provides safe truck entry staging for processing at a new guard house. New truck drives extend from the guard house to east and west sides of the food plant. The truck drives also provide access to the project’s other exterior improvements including; a process wastewater treatment building, a refrigeration building, a firewater pump house, truck trailer staging, etc.
- A new employee entrance that is located just north of the new truck entrance. The new drive has access control adjacent to the guard house. The drive extends from the access control to a new employee parking lot located adjacent to the south end of the new building expansion. Safety measures were implemented to maintain separation of employee and truck traffic.
- The new plant is designed in a classic C shaped flow from receiving to blending to cooking to packing to shipping. This minimizes the times ingredients/products will cross over their previous path reducing traffic and clutter. The receiving dock is on the northeast corner of the facility, preparation and blending flow from west to east, forming and cooking happens in one of three independent halls traveling from north to south, packing and storage move from east to west and shipping happens on the west side of the building.
- Three production halls that contains six fully cooked lines, each with a nominal capacity of 5,000lb/hr. or 120 Million lbs./yr. Additionally, the plant houses the largest Armor Inox line in the nation capable of producing 100 Million lbs. annually.
- Estimated facility capacity when full: 400,000 lbs./wk.; 2,000,000+ lbs./yr.
- State-of-the-art WWT process that includes: 70,000-gallon pit, 3 DAFs, 1 Micro System, 250,000-gallon EQ tank.
- Investment in state-of-the-art technology to build a “Factory for the Future”, connect its machines to the Industrial Internet of Things (IIoT) and further improve the safety of its employees and the products manufactured.
- The facility has plenty of area for learning centers, team rooms and KPI discussions, which are in addition to the normally expected welfare areas. The teams are being trained on engagement techniques using the Engagement Model developed by the Opx Team sponsored by PMMI. This model will be instituted in this facility and then moved out to the 5 sister campuses.
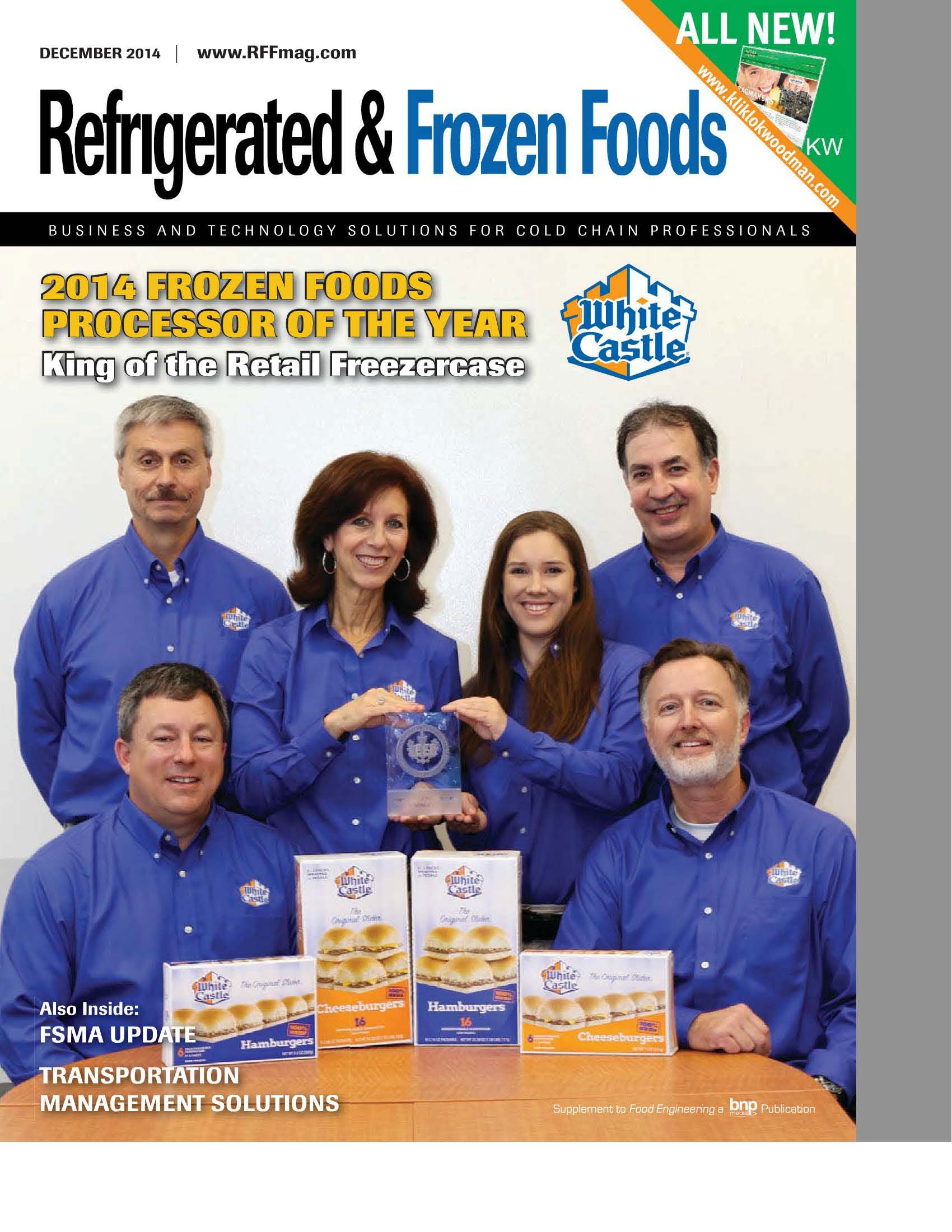
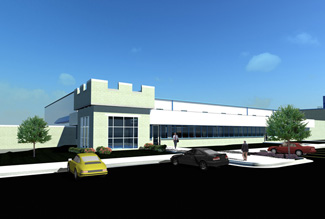
Refrigerated & Frozen Foods Magazine – Frozen Foods Processor of the Year
White Castle – Vandalia, Ohio
White Castle’s latest state-of-the-art processing plant has been named 2014 Frozen Foods Processor of the Year by Refrigerated and Frozen Foods magazine. Located in Vandalia, Ohio, the 93-year-old, family-owned company opened this new $19.4 million, 80,000 square foot, and highly sustainable LEED Gold Certified food manufacturing facility in November 2014 to meet the demand for its retail frozen food offerings. The innovative design of the new facility’s processes produces 3.5 million pounds of USDA-inspected raw ground beef into sandwiches, equally close to 16,500 burgers per hour, 220,000 sandwiches a day and over 57 million sandwiches per year. White Castle’s cheeseburger reigns as the No. 1 selling frozen sandwich in retail stores and vending operations across the country, earning its recognition as King of the Retail Freezer case.
The Frozen Foods Processor of the Year honor is awarded each year by Refrigerated and Frozen Foods Magazine to a Plant that describes in 1,000 words or less, how it continues to enforce food safety, energy efficiency and new product development, all while going above and beyond industry standards. Facility Design Group (FDG) nominated its White Castle project for the award this year.
White Castle was awarded the LEED Gold Certification due to its ability to meet the U.S. Green Building Council’s (USGBC) requirements in multiple categories including sustainable sites, water efficiency, energy and atmosphere, materials and resources, indoor environmental quality, and innovation and design process. The USGBC’s LEED certification program is the national standard in the rating of green buildings. While LEED certification is not required to be named Food Processor of the Year, it shows the depth of White Castle’s commitment to the environment with every aspect of the new facility. White Castle demonstrates its commitment to improving the quality of the communities where they operate and in finding innovative ways to minimize their impact on the environment.
Much of the project’s success stems from the collaborative nature of its planning and implementation processes. The Vandalia, Ohio plant was designed with Facility Design Group (FDG), an Atlanta-based Architecture & Engineering firm, utilizing the firm’s Collaborative Approach to projects. This approach allows for the integration all members of the project team including the Owner, Program Manager, Project Architect, Consultants and Trade Contractors during both the planning and implementation phases of the project. This unique approach allowed for seamless integration throughout the entire course of the project and resulted in a completed facility that exceeded many of the project’s goals. This new facility – from automated machinery to energy efficient processes – brings White Castle a long way since its start in 1921 with a castle shaped restaurant and the five-cent small burger. No doubt, their many fans – called Cravers – will continue to grow in number.